Apron Plate Band
Dryer
A band dryer is an industrial drying apparatus used to remove moisture or solvents from various materials in a continuous, controlled, and efficient manner using a conveyor belt system.
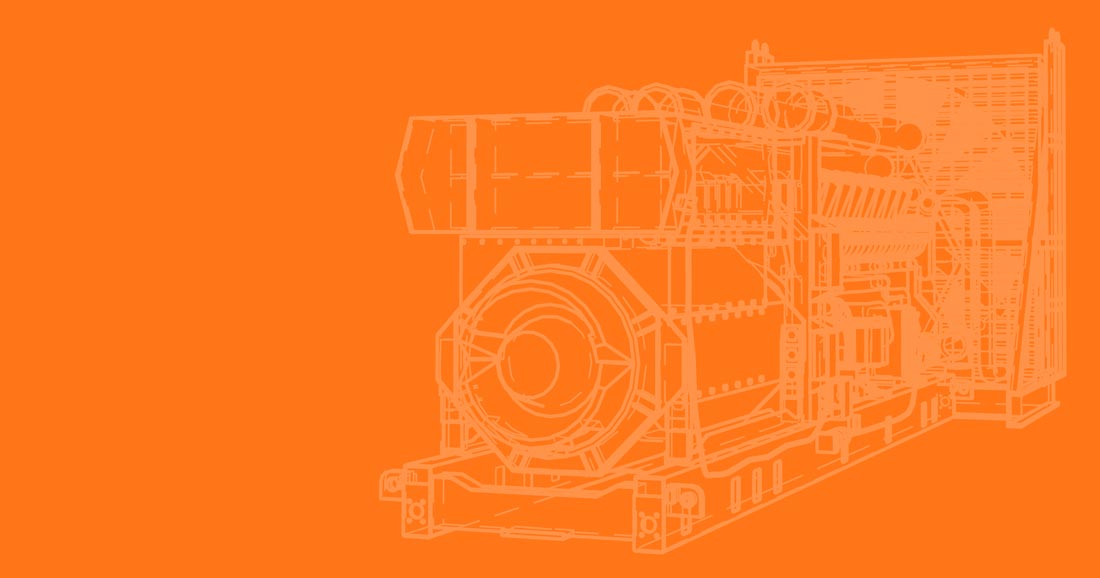
AN ADVANCED DRYING SOLUTION
Precision Drying Solution
In today’s competitive food processing industry, maintaining the highest quality of dried food products while optimizing production costs and environmental sustainability is paramount. The GEM Apron Band Dryer emerges as the definitive solution, addressing the growing demand for high-quality dried products that retain the authenticity and characteristics of fresh ingredients.
What is a Band Dryer?
A band dryer is a type of continuous dryer used in various industries to dry materials such as food products, chemicals, pharmaceuticals, and agricultural products. It consists of a conveyor belt that moves the material through a heated chamber, where drying occurs through convection and sometimes radiation.
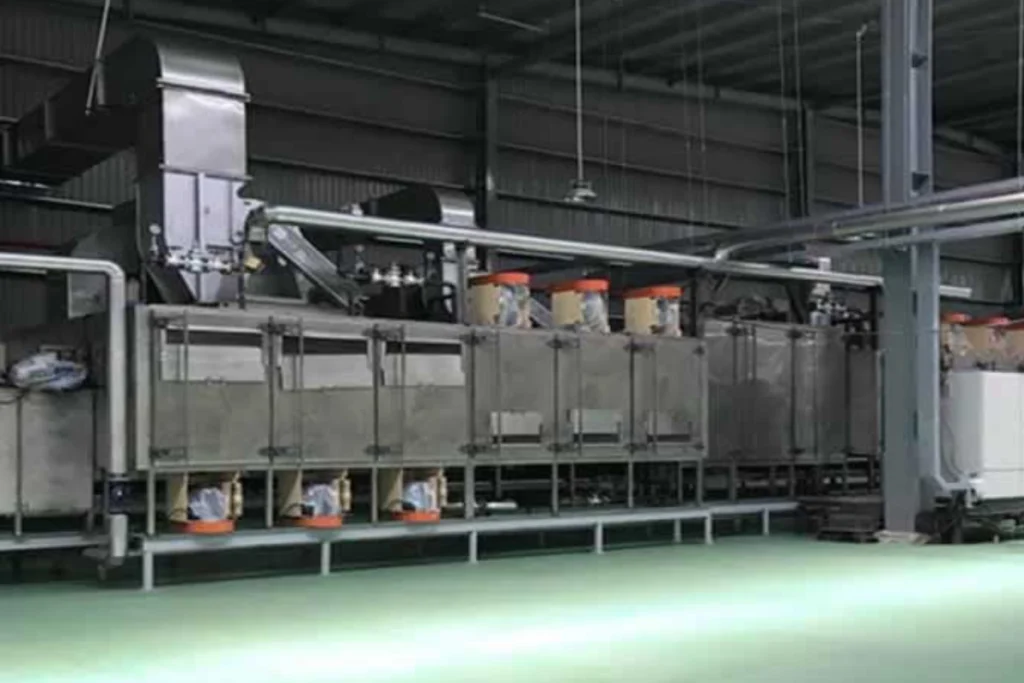
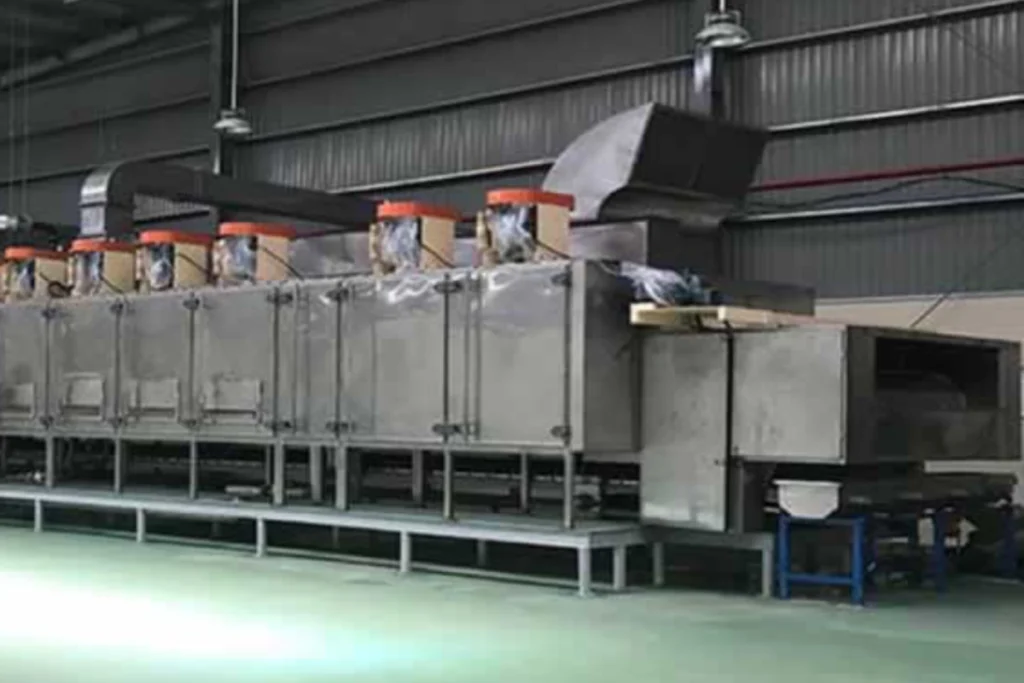
Working Principle of a Band Dryer
2-STAGE BAND DRYER (Cross-Sectional Views)
Salient Features
- Complete product uniformity using multiple airflow direction change
- Efficient air circulation system
- Cost-effective
- Minimal Heat Loss
- Heat recovery systems to re-utilize exhaust heat
- Continuous fine collection and removal
Advantages
- Product Quality Preservation: Multi-zone temperature controls prevent overheating and case hardening, maintaining the intrinsic qualities of the dried product.
- Operational Efficiency: Turbine-type fans with variable speed drives ensure minimal power consumption while delivering optimal performance.
- Energy Optimization: Advanced heat recovery systems can repurpose exhaust heat, either returning it to the dryer or providing energy for other processing equipment..
- Comprehensive Drying: Carefully engineered transfer zones minimize product sticking, agglomeration, and breakage, ensuring superior processing outcomes..
- Space Effciency: Compact design with a high throughput capacity, making efficient use of floor space in industrial settings...
- Controlled Environment: Ability to control drying parameters such as temperature, airflow, and residence time ensures optimal drying conditions for different materials.
Specifications
- Capacity up to 1600 Kg/h of finished product
- Independent multi-zone temperature controls
- Multi-zone airflow pattern
- Complete PLC and SCADA systems for control and instrumentation
Process Flow Diagram
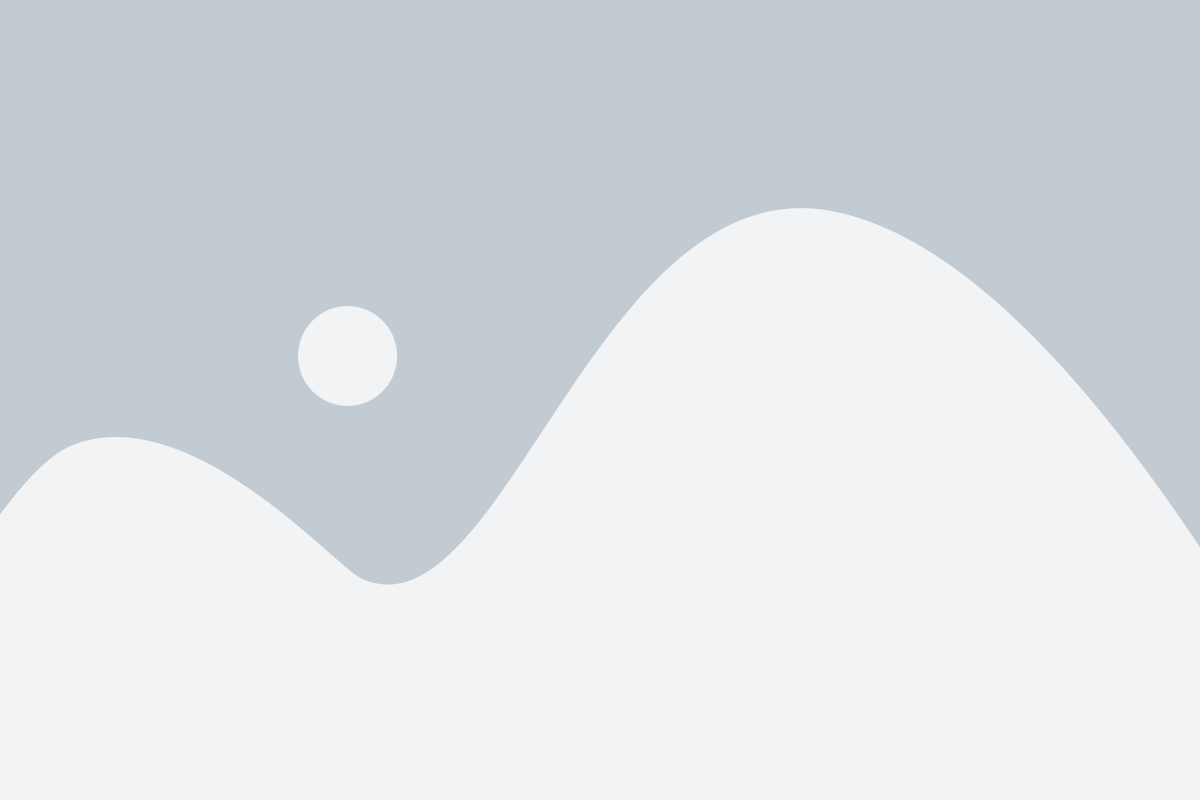
Factors Affecting Drying Rate
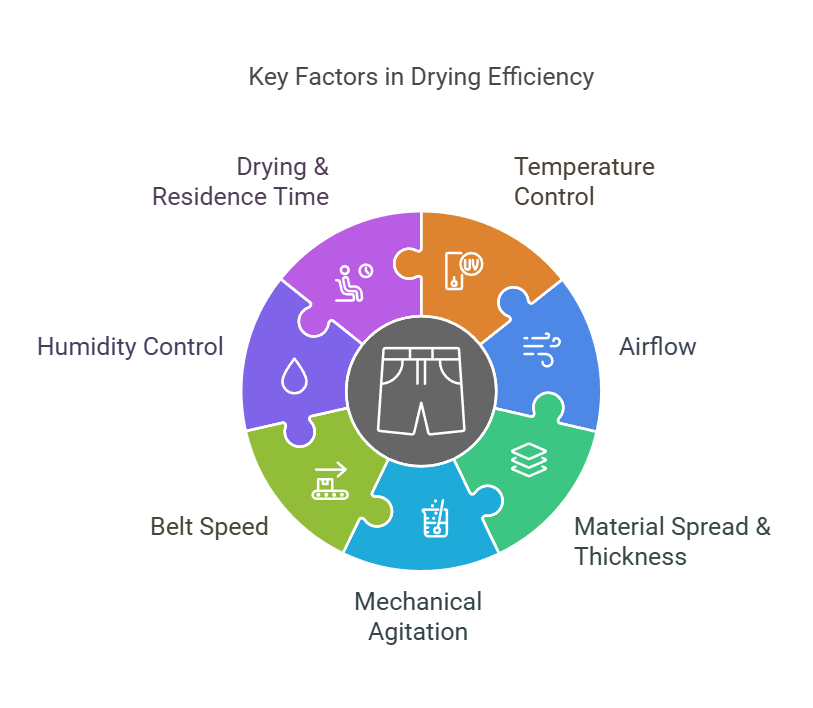
Application
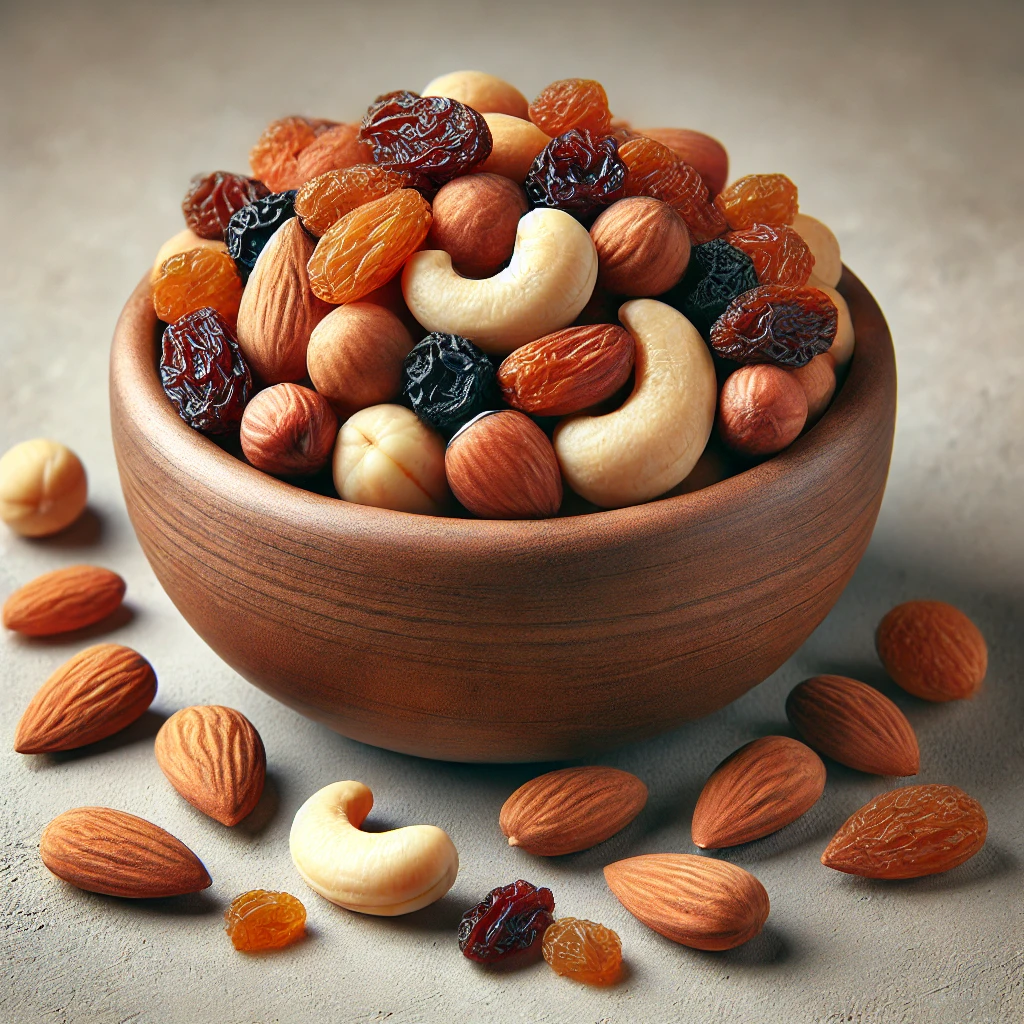
Dry Fruits
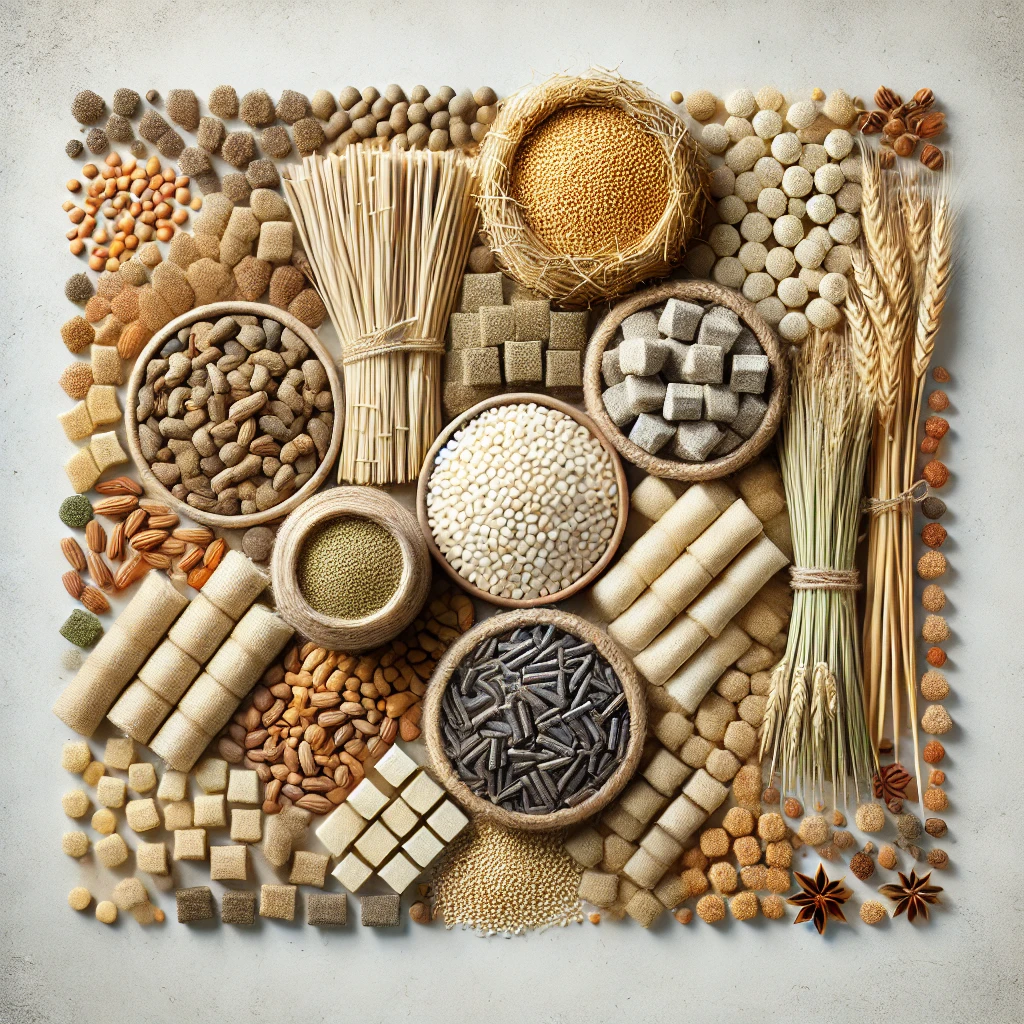
Animal Feeds
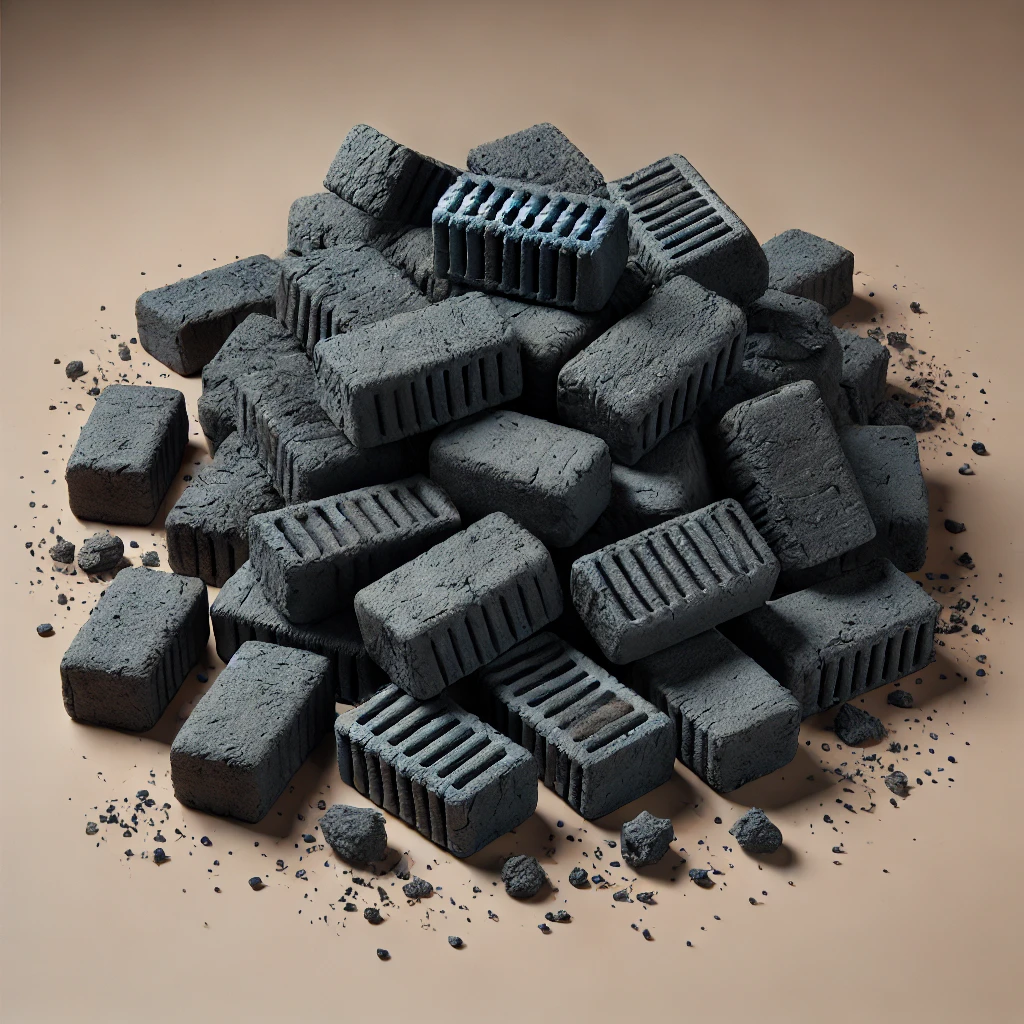
Coal Briquettes
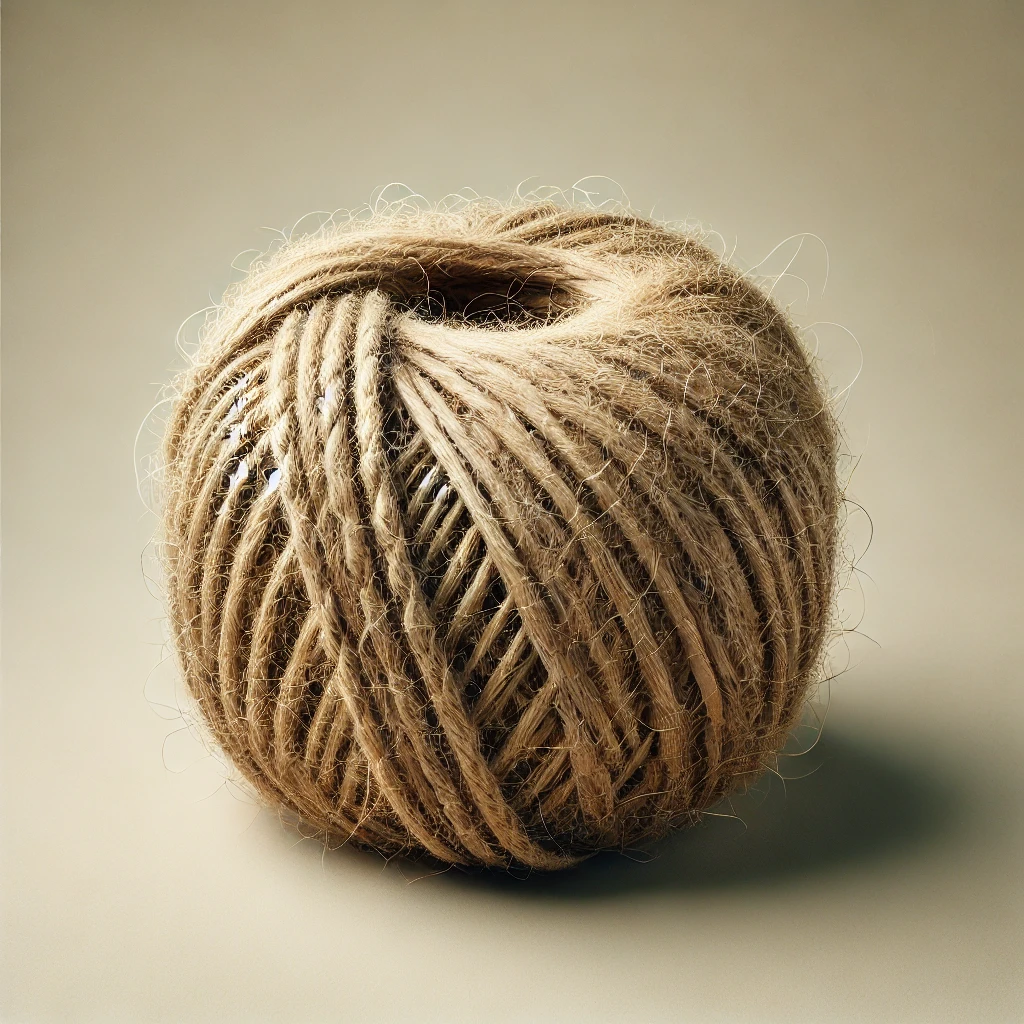
Natural & Synthetic Fiber
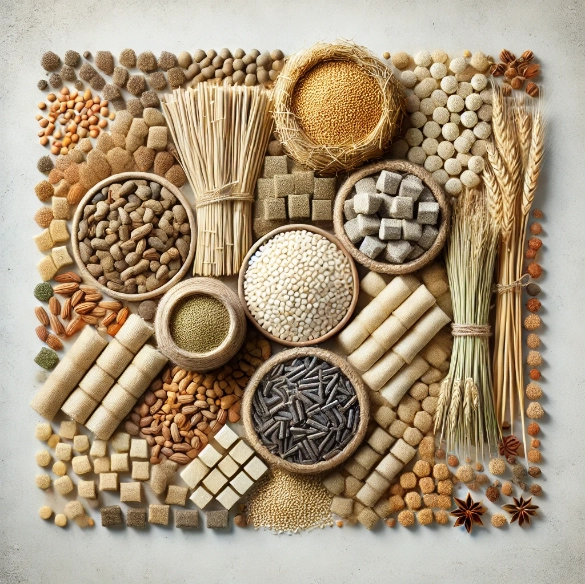
Cereals
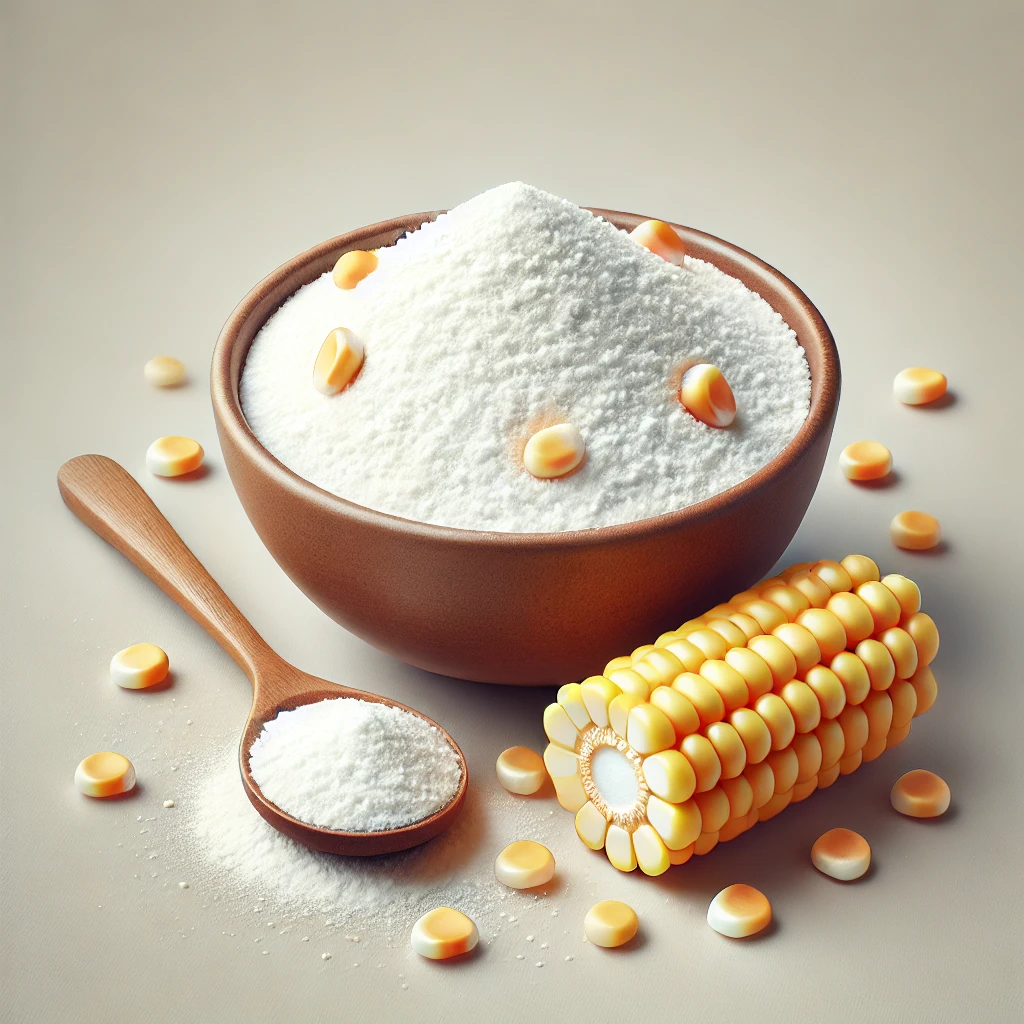
Corn Starch
Have Questions ?