PAddle Dryer
The Paddle Drier utilizes the conduction mode of heat transfer, ensuring exceptionally high thermal efficiency. It accomplishes the drying of powdery, crystalline, or granular materials by introducing them to revolving cuneiform hollow paddles, employing steam, water, or oil as a heating medium.
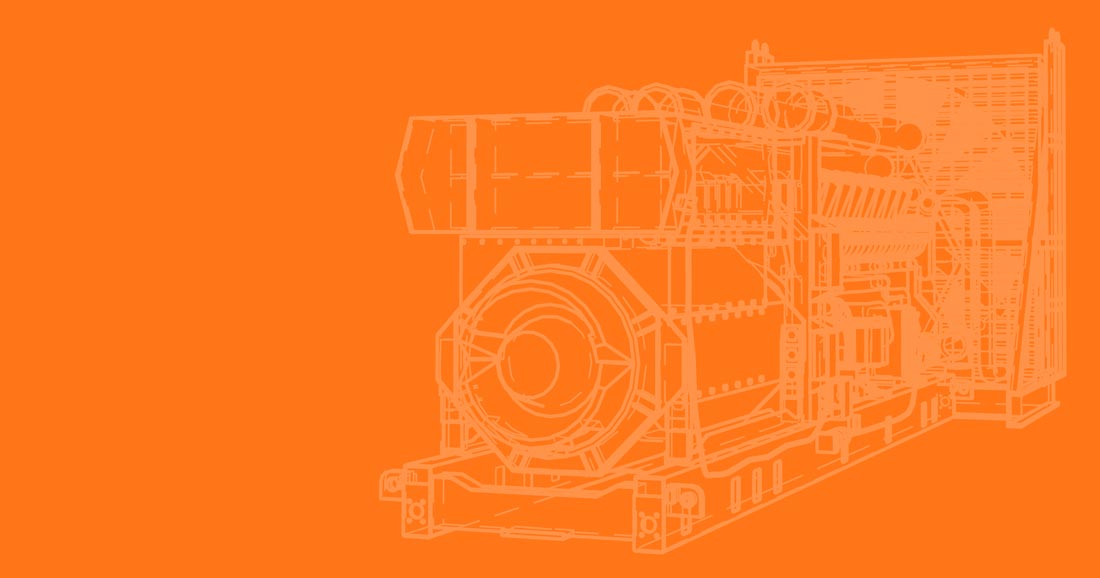
ADVANCED DRYING SOLUTION by
GEM
What is a Paddle Dryer?
An indirect conduction heating device, paddle dryer is perfect for drying materials like paste, powder, and granules that have high thermal stability. This dryer works by using revolving paddles or blades that come into contact with the sludge particles and are heated outside. In order to continually supply the drying surface, two or four sets of blades typically revolve concurrently, cutting into and stirring the solid lumps of sludge into smaller particles. Paddle dryers may function without the requirement for back-mixing because the revolving paddles create enough agitation to stop sticky sludge from forming.
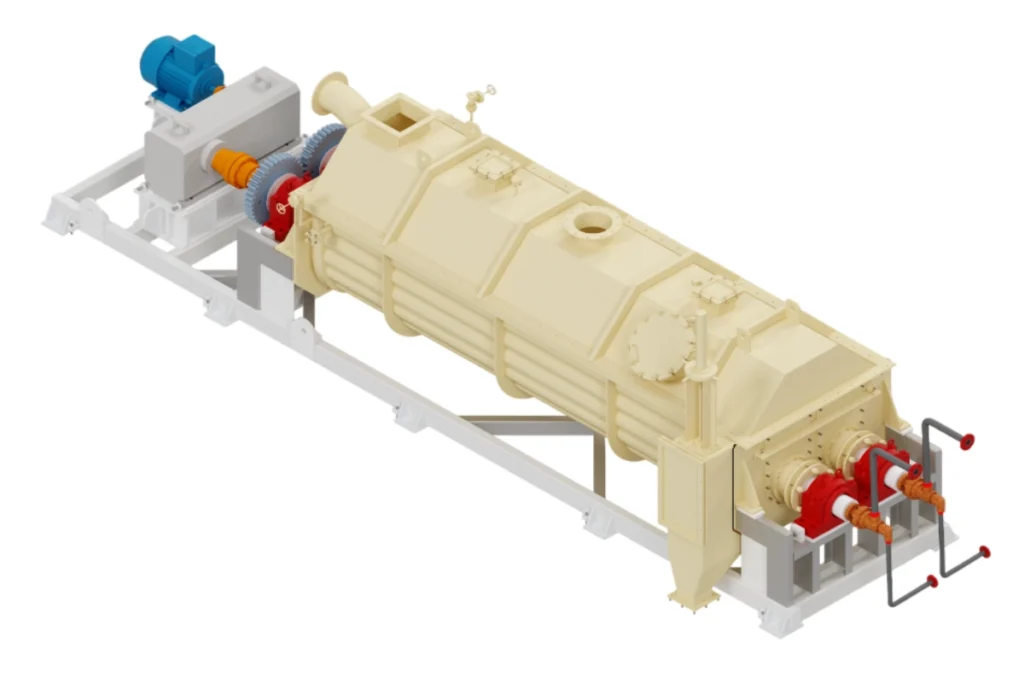
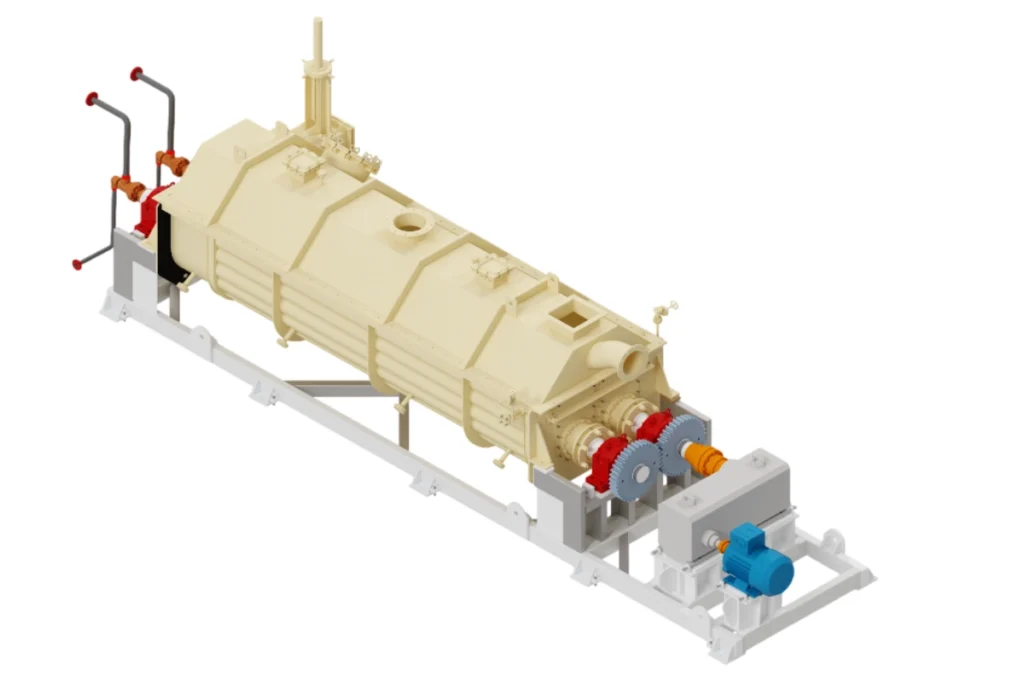
Working Principle of a Paddle Dryer
The paddle dryer is a continuous heat transfer system used for drying materials. It features thermal shafts with rotating hollow paddles within a jacketed trough. Steam introduced into the shafts heats the paddles, which agitate and transfer heat to the material, ensuring effective drying.
Heated scavenging air, supplied by the Forced Draft (FD) fan, removes moisture from the drying chamber. The exhaust air, containing moisture and particulates, is first cleaned in a Cyclone Separator, with fines discharged through a rotary valve. Remaining particulates are further removed in a Dip Type Scrubber using water, and the saturated air is vented to the atmosphere.
Pressure control is maintained by the Induced Draft (ID) fan, while temperature is regulated at approximately 105 ºC by the Temperature Indicator Controller. The system operates semi-automatically with local control panel management.
Salient Features
- Unique Heat Transfer Design
- Advanced Paddle Configuration
- Versatile Material Handling
- Process Control & Efficiency
- Construction & Maintenance Features
- Vacuum Operation Capability
- Consistent Final Moisture Content
- Multiple feed and Discharege Options
- Can handle varied feed characteristics
Advantages
- Achieves over 90% thermal efficiency with minimal heat loss in the conduction system.
- Minimizes utility consumption, including steam, thermic fluid, and power, leading to reduced operating costs for drying.
- Significantly reduces sludge weight and volume, lowering transport costs and environmental impact.
- Features a compact design compared to belt and rotary dryers, offering a large heat transfer area in a small footprint.
- Handles sludge with up to 90% water content (10% dry solids) and dries it to below 5% water (95% dry solids) without back mixing.
- Decreases the size and cost of downstream equipment, such as cyclones, filters, fans, and ducts.
- Mechanical agitation by paddles effectively manages viscous or sticky materials that challenge other dryers.
- Complies with environmental regulations by producing ‘A’ class bio-solids.
- Enhances calorific value of sludge through moisture reduction, improving incineration efficiency without extra fuel.
- Eliminates landfill needs, creating marketable products as alternative fuel through efficient sludge drying.
- Prevents spillage and odours in the ETP area while drying sludge.
Major Equipments
Paddle Dryer: Main unit where material is dried using heat from thermal shafts and paddles.
Air Heater: Warms scavenging air before it’s supplied to the dryer system.
Cyclone Separator: Separates fines from exhaust air.
Rotary Valve: Discharges fines collected in the cyclone separator.
Forced Draft (FD) Fan: Supplies scavenging air to the dryer.
Induced Draft (ID) Fan: Maintains balanced or negative pressure in the system.
Gearbox: Transmits motor power to the thermal shafts.
Dip Type Scrubber: Removes dust from exhaust air using water.
Drive Motor: Powers the thermal shafts in the paddle dryer.
Temperature Indicator Controller (TIC): Controls and monitors product temperature.
Induced Draft (ID) Fan: Maintains balanced or negative pressure in the system.
Control Valve (TCV): Regulates temperature by adjusting steam flow based on TIC.
Control System: Semi-automatic system for operating the dryer, including motor controls.
Nature of Flow inside the Paddles
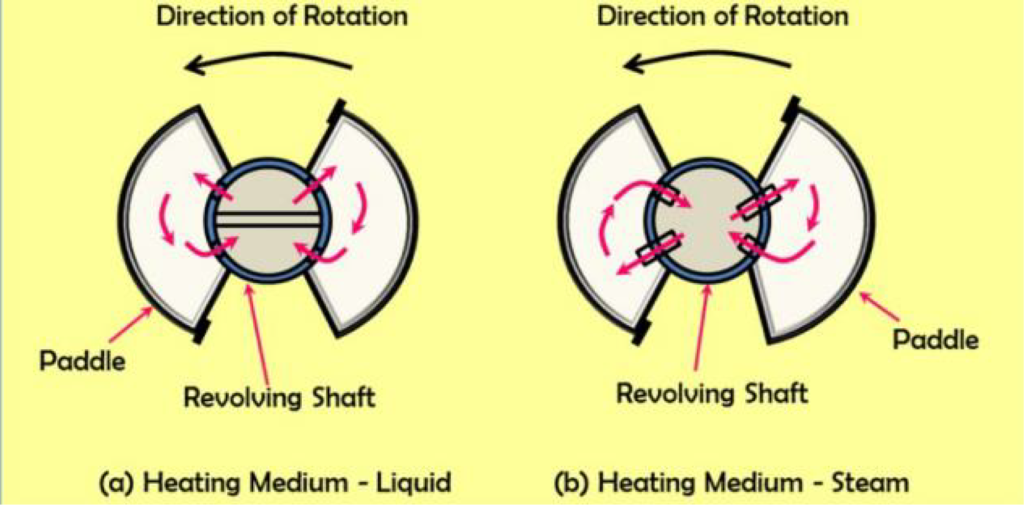
The heating medium flows into a hollow shaft, through flow holes into hollow paddles, and exits through outlet holes into the collection half of the shaft before leaving the component.
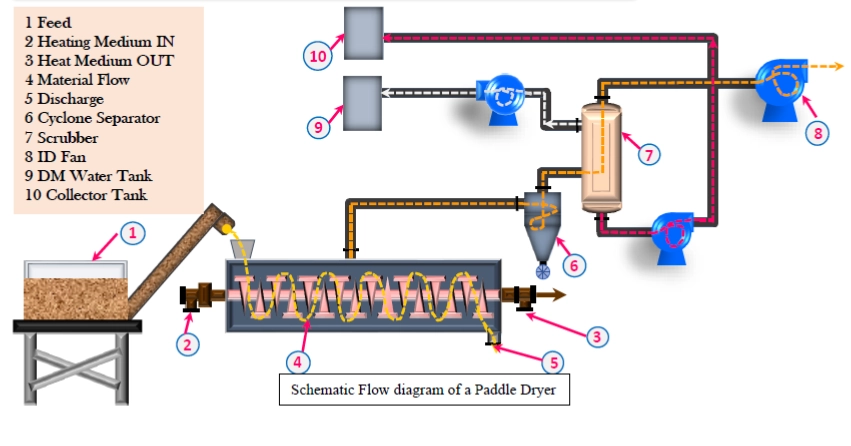
Specifications
- System Capacities: Ranges from small to large plants.
- Heat transfer areas: 2.5 to 250 m²
- Rotational speed of the shaft: 10-20 RPM
- Residence time ranges
- Heat transfer distribution: 23% through jacket, 77% through paddle
- Low temperature drying for heat sensitive material using vacuum
- The heat transfer medium for the paddle dryer can be steam, thermic fluids.
- Material of construction is based on the pH of the sludge.
- Scavenging air carries out the water vapour to the exhaust thus avoiding condensation inside the dryer
Process Flow Diagram
Major Parts of a Paddle Dryer
Factors Affecting Drying Rate
Application
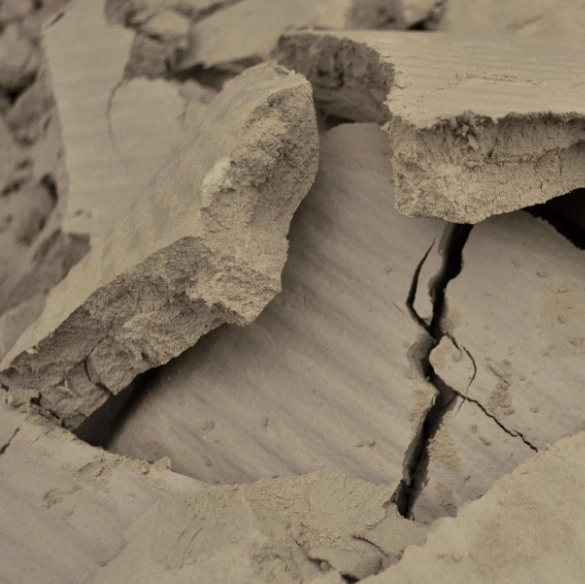
Filter Cakes
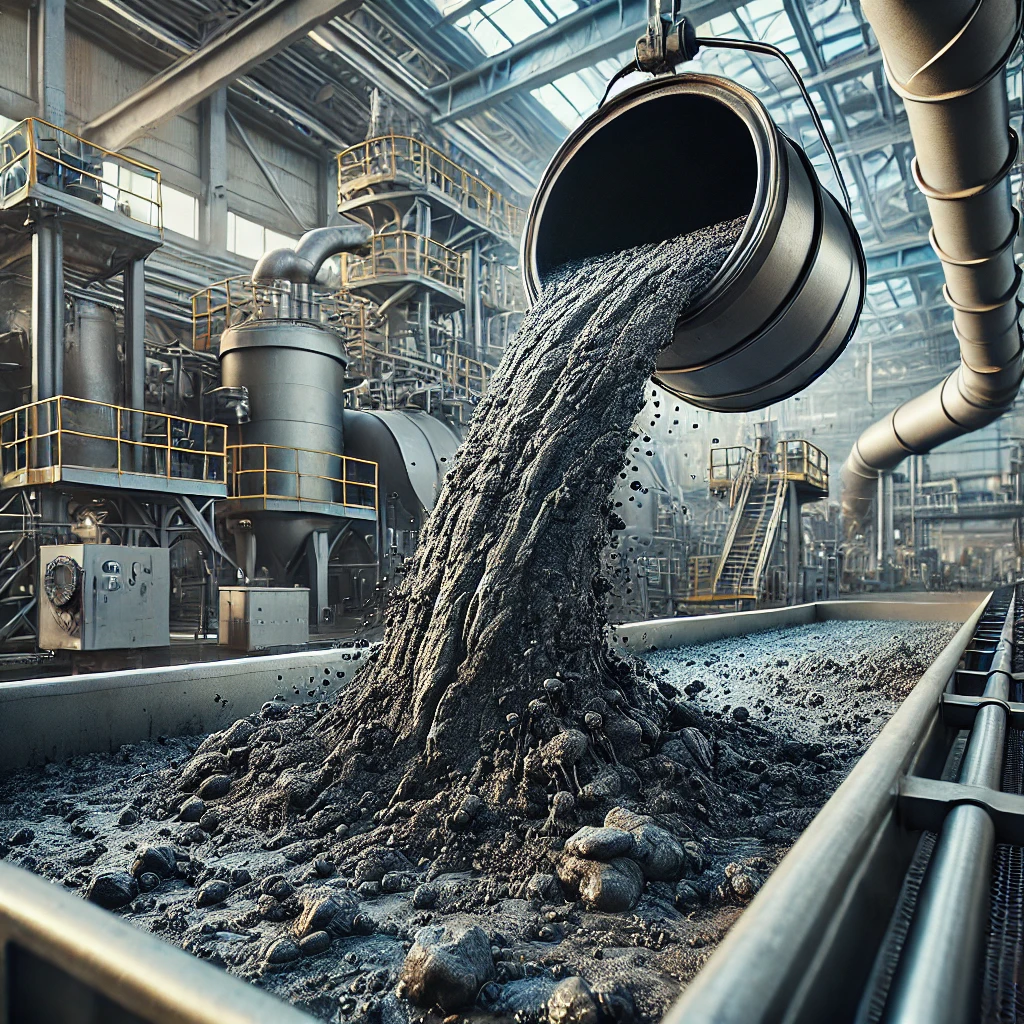
Slurry
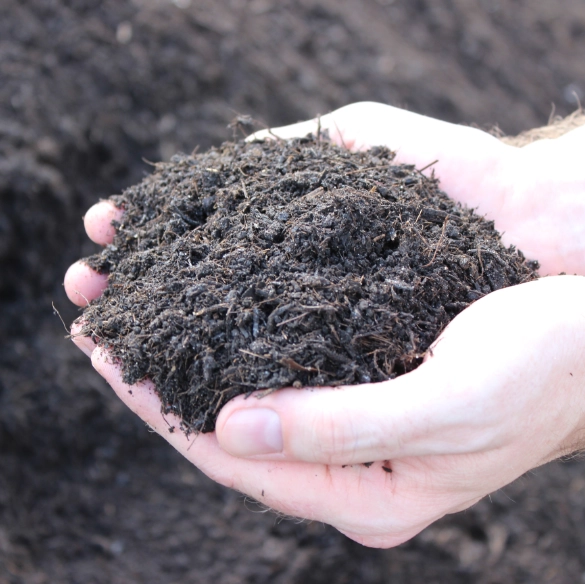
Bio-Sludge
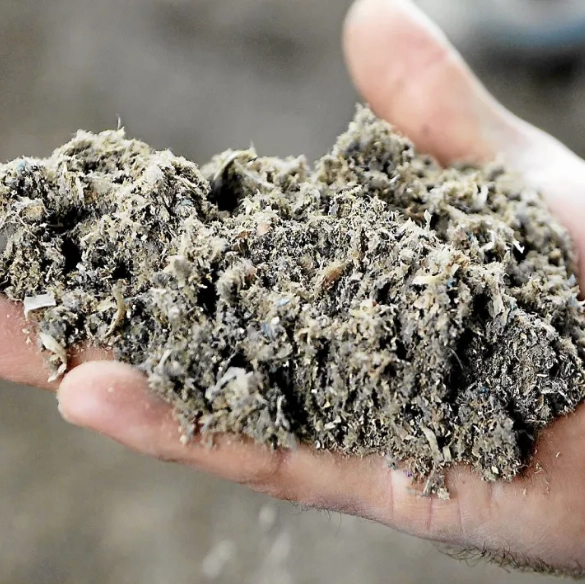
Paper Sludge
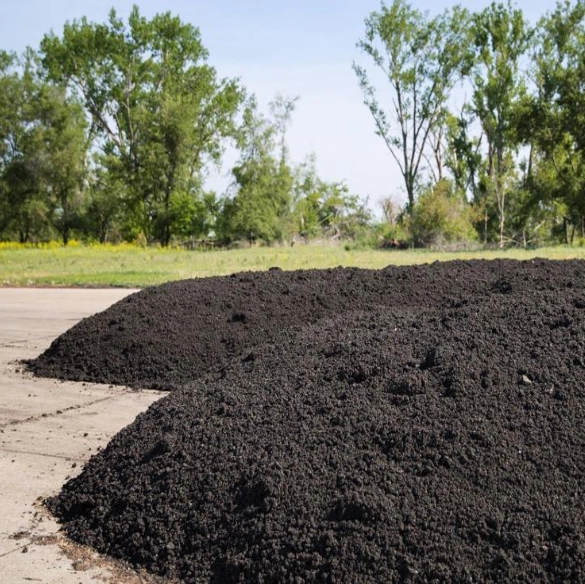
WTP Sludge
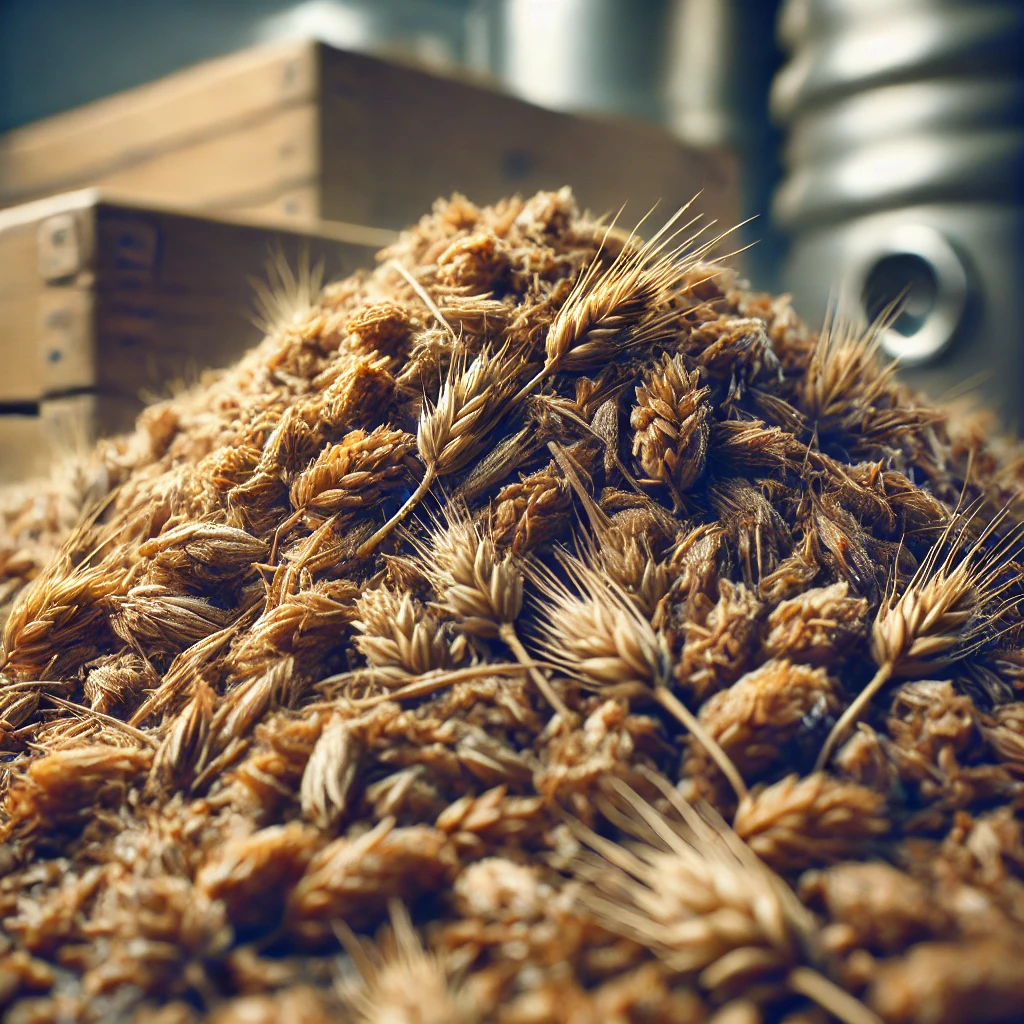
Spent-grains from brewary
Have Questions ?