Rotary Dryer
Rotary dryers represent a pinnacle of industrial drying technology, offering unparalleled flexibility in processing bulk solid materials across a wide range of industries. These robust machines have become an essential solution for businesses seeking efficient moisture removal, demonstrating remarkable adaptability in handling diverse materials and industrial applications.
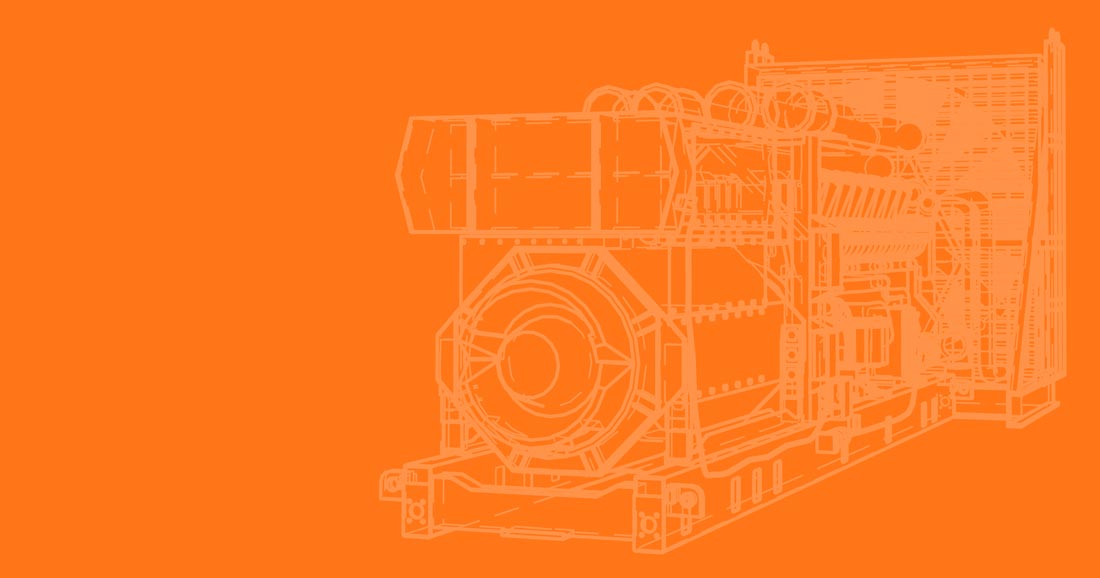
AN ADVANCED DRYING SOLUTION
A Versatile Industrial Drying Technology
Rotary Dryers are flexible in processing virtually any bulk solid material, rotary dryers have made their way into an abundance of industries around the globe.
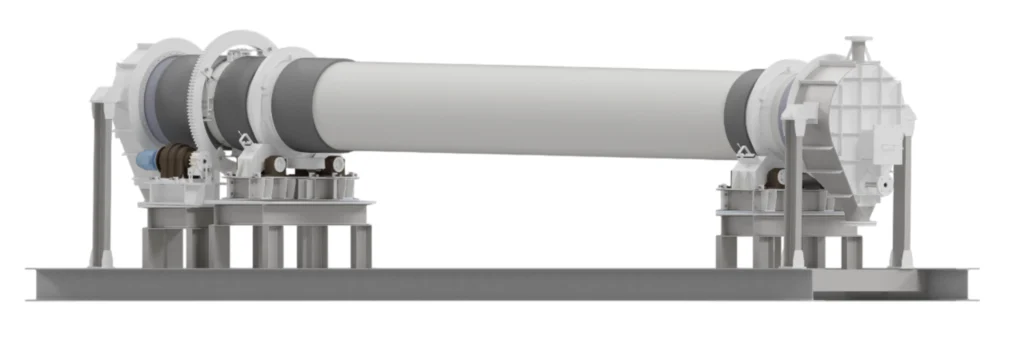
What is a Rotary Dryer?
Working Principle of a Rotary Dryer
A rotary calciner operates by utilizing a rotating cylindrical drum, which is inclined slightly to facilitate the movement of material from the higher to the lower end. The process begins with raw material being introduced into the drum, which rotates slowly, ensuring thorough mixing and uniform heating. Heat is supplied either through external burners or indirect heating systems, and the material is subjected to high temperatures ranging from 500°C to 1500°C, depending on the specific application. This rotation and heating facilitate various thermal processes such as calcination, sintering, and chemical reactions, resulting in the desired product transformations.
As the material progresses through the heated section of the drum, it undergoes thermal decomposition or other chemical changes. Once processed, the material moves into a cooling zone where it is gradually cooled to prevent unwanted reactions and make it ready for further handling. The rotary calciner’s advanced control systems manage temperature, rotation speed, and material flow to ensure efficient operation. Emissions are carefully controlled through gas handling systems to minimize environmental impact. This continuous, controlled processing makes the rotary calciner an essential tool in industries like cement production, metallurgy, and chemical processing.
Types of Rotary Dryers
Rotary dryer is of two types:-
1. Direct Rotary Dryer preferred to dry the high density bulk solids. There is direct contact between the material and drying air. It results more consistent and uniform property of the product. To increase the rate of heat transfer internal flights are used. Here Convection and Radiation mode of heat transfer are more dominated.
2. Indirect Rotary Dryer best suited to dry dusty and fine materials such as grain, pulps mostly which is a heat sensitive materials. The material and drying air separated by drum shell. Drum shell is heated externally through air by burner which is fitted in Furnace Shroud. Here Conduction and Radiation mode of heat transfer are more dominated:-
- Conduction: Heat is transferred by conduction from the heat source to the material through drum shell.
- Radiation: The heated drum shell emits thermal radiation in the form of infrared waves which directly heat the material.
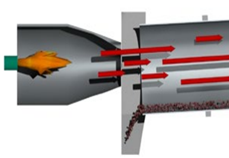
Direct Rotary Dryer
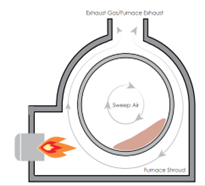
Indirect Rotary Dryer
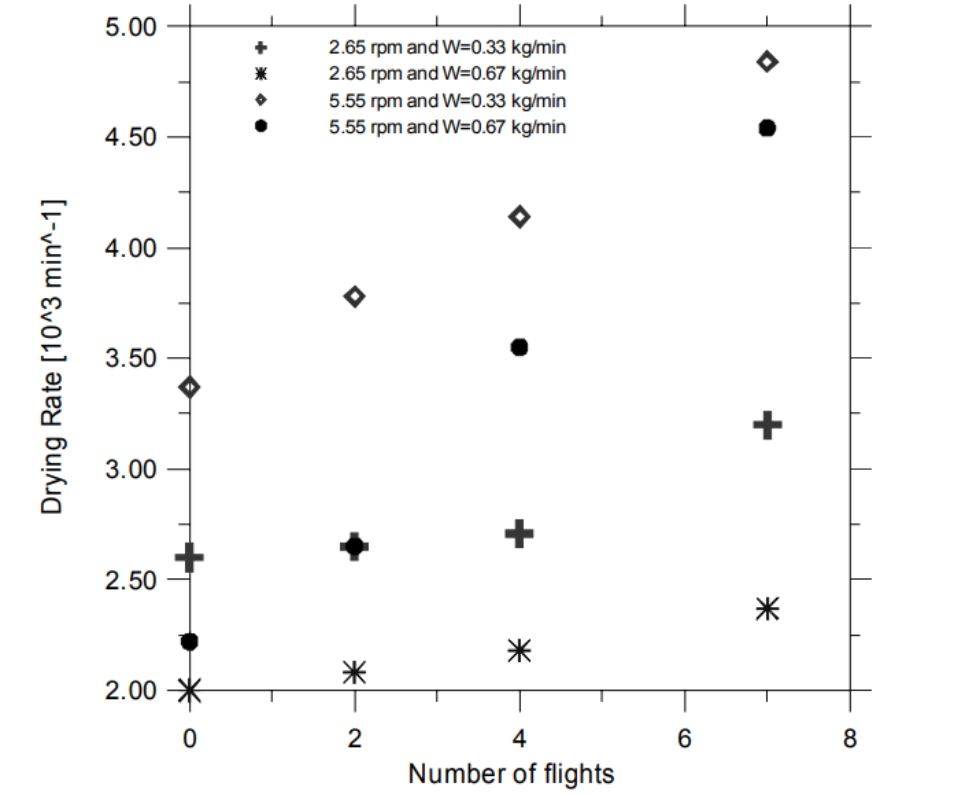
Variation in drying rate with number of flights
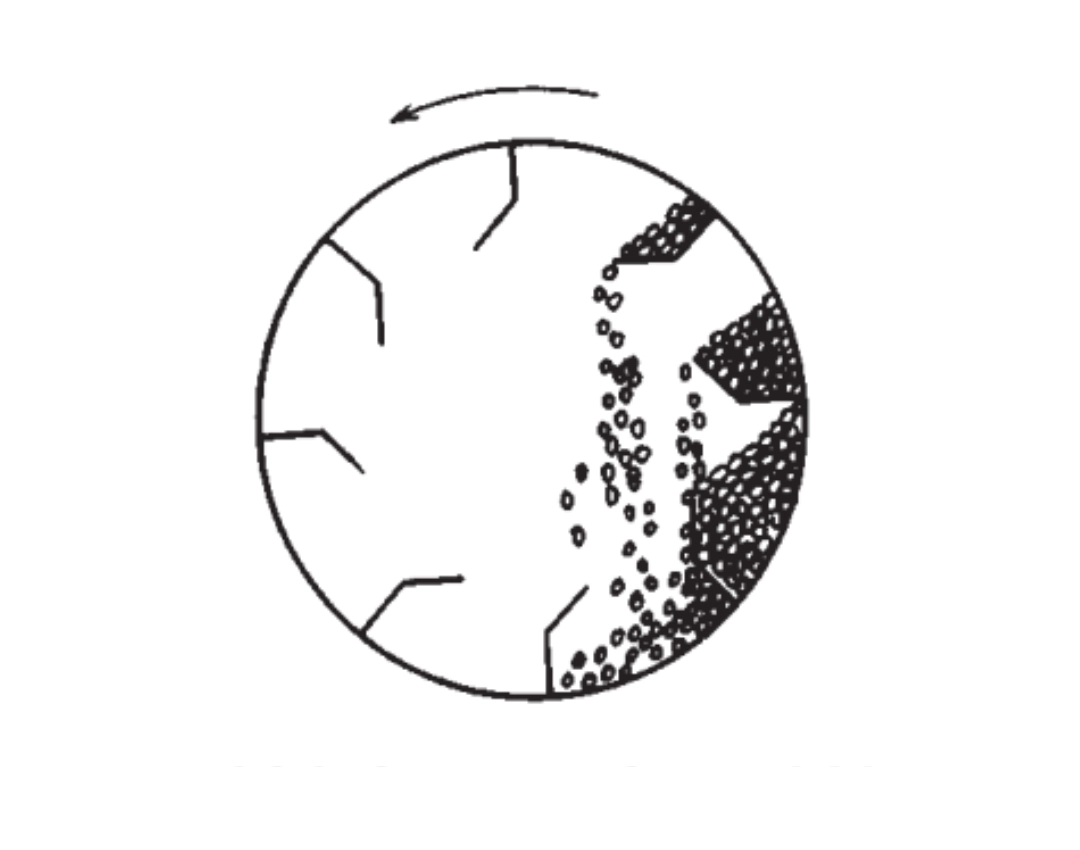
Movement of materials inside the rotary dryer
Salient Features
- Rotating Drum
- High-Temperature Operation
- Continuous Processing
- Heat Source
- Cooling Zone
- Hygienic design
Advantages
- Continuous Operation: Rotary dryers provide continuous processing, which enhances overall efficiency and throughput compared to batch dryers.
- Effective Heat Transfer: The rotating drum ensures thorough and uniform heat transfer to the material, optimizing drying performance.
- Wide Range of Materials: They can handle a variety of materials, including granular, powdered, and pelletized substances, making them suitable for numerous industries..
- Adaptable to different feed sizes:Rotary dryers can process materials of various sizes and moisture content levels.
- Uniform Drying: The rotating action and the internal lifting flights provide a thorough mixing of the material, ensuring consistent drying and preventing overheating or under-drying.
- High Capacity: Rotary dryers are capable of handling large volumes of material, which is ideal for high-capacity production processes.
- Energy Efficient: Some rotary dryers are equipped with heat recovery systems to capture and reuse energy, improving overall efficiency and reducing operational costs.
Specifications
- Drying capacity of up to 150 tonnes can be achieved
- Both indirect and direct type of heating is possible
- Fuels that can be used are Natural gas, Light Diesel Oil, Electrical heating
- Diameter of the Rotary Dryer up to 4 meters
Process Flow Diagram
Factors Affecting Drying Efficiency
Applications
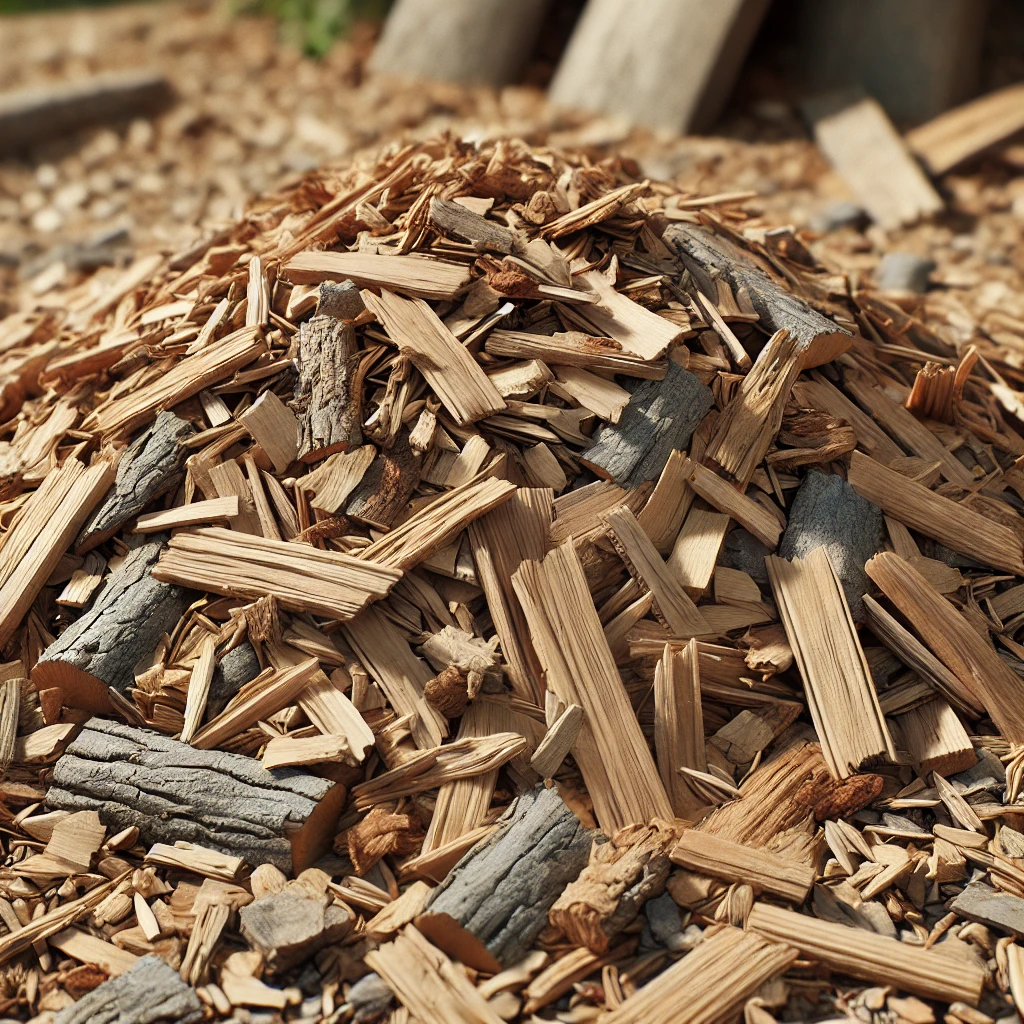
Wood Chips
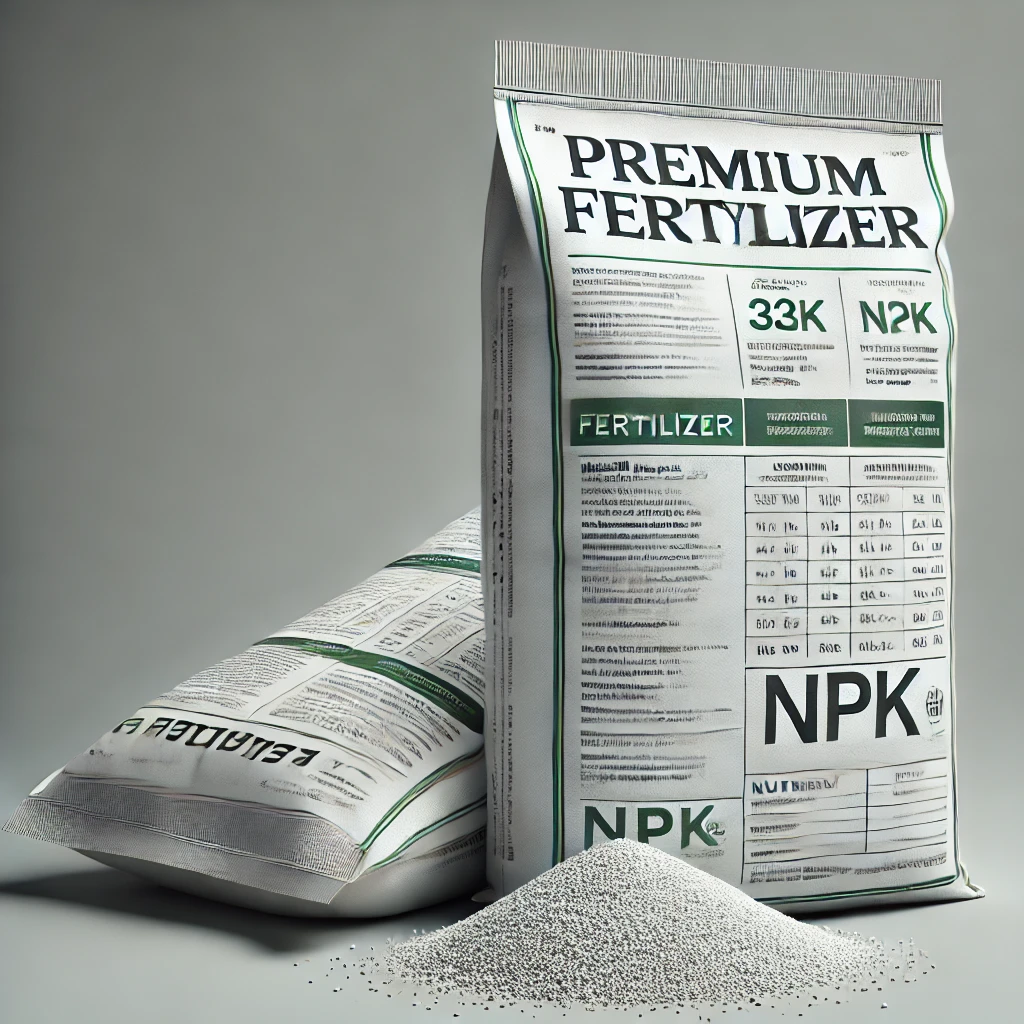
Fertilizers
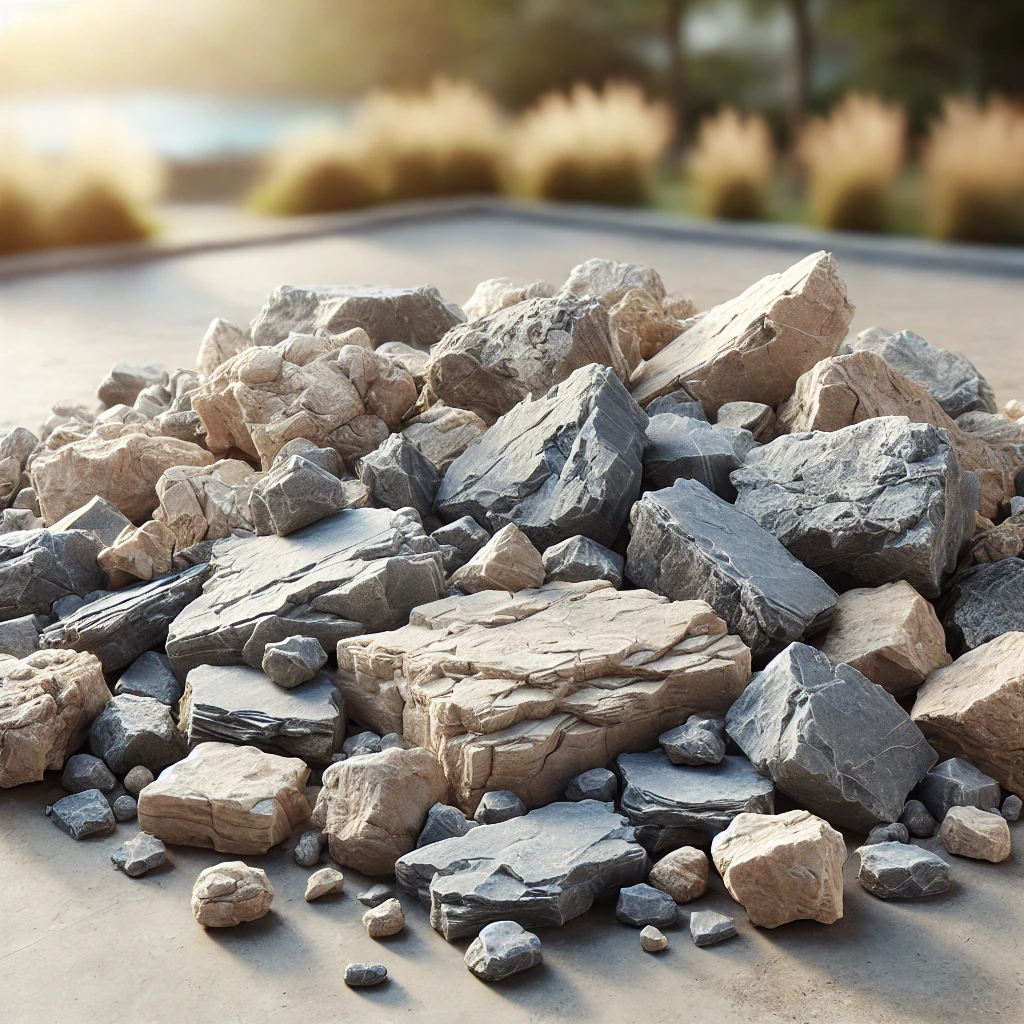
Lime Stones

Ores
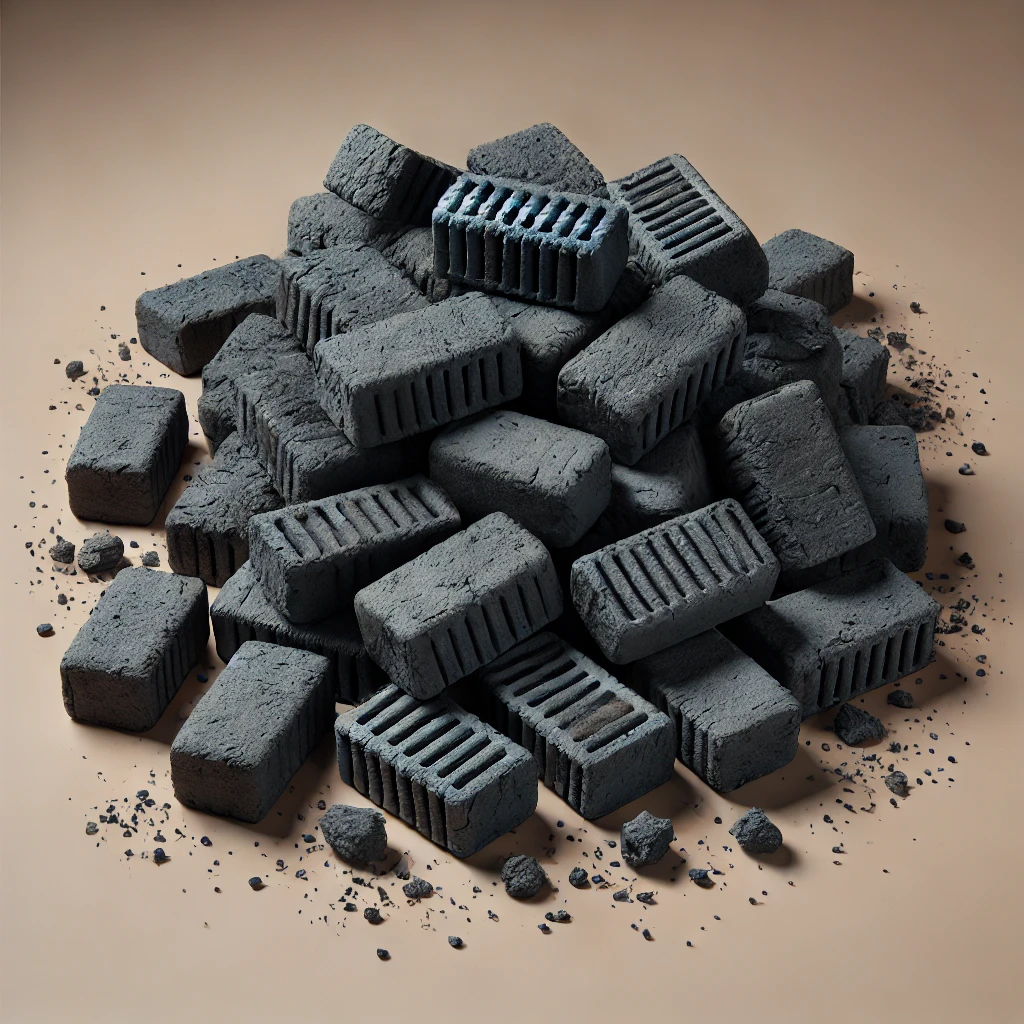
Coal
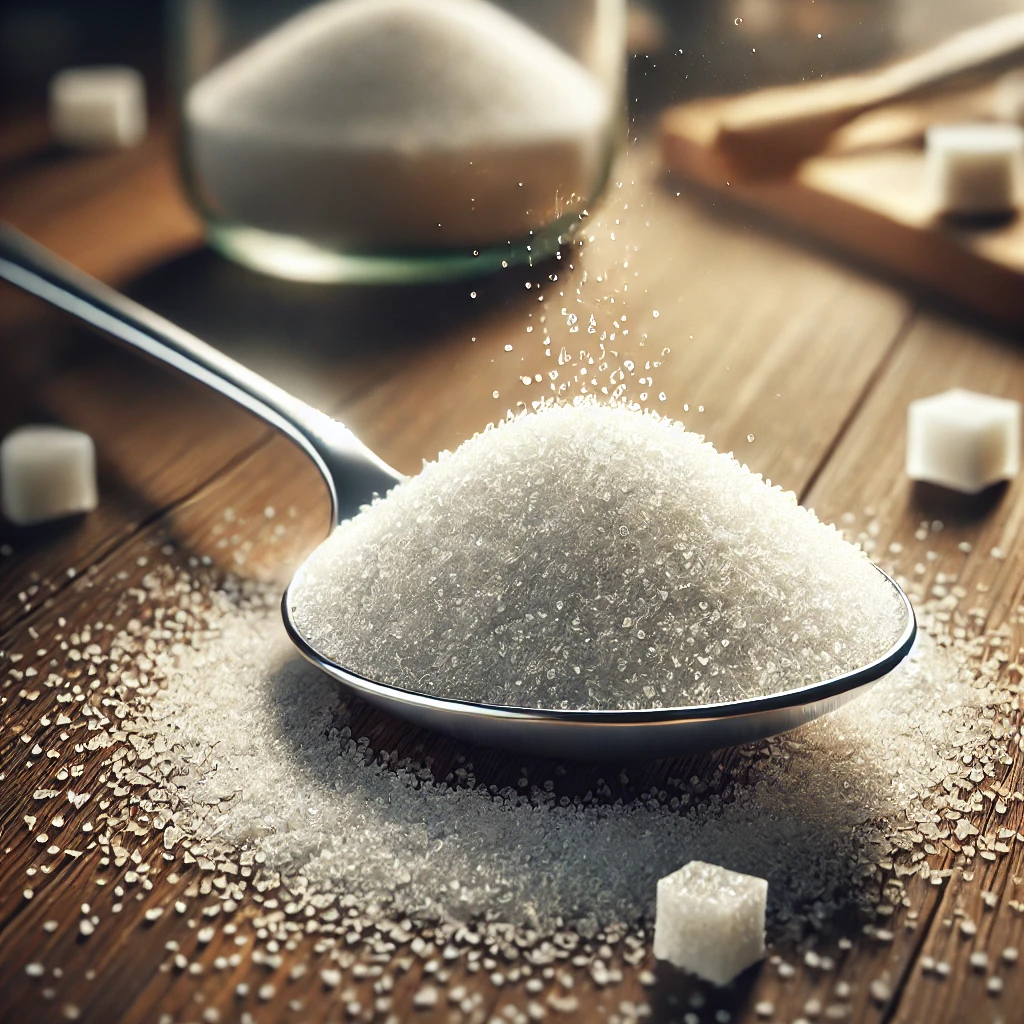
Sugar
Have Questions ?