Tunnel Dryer
The material enters one end of the tunnel and moves slowly through different temperature zones, emerging dried at the other end. This creates an efficient, continuous drying process
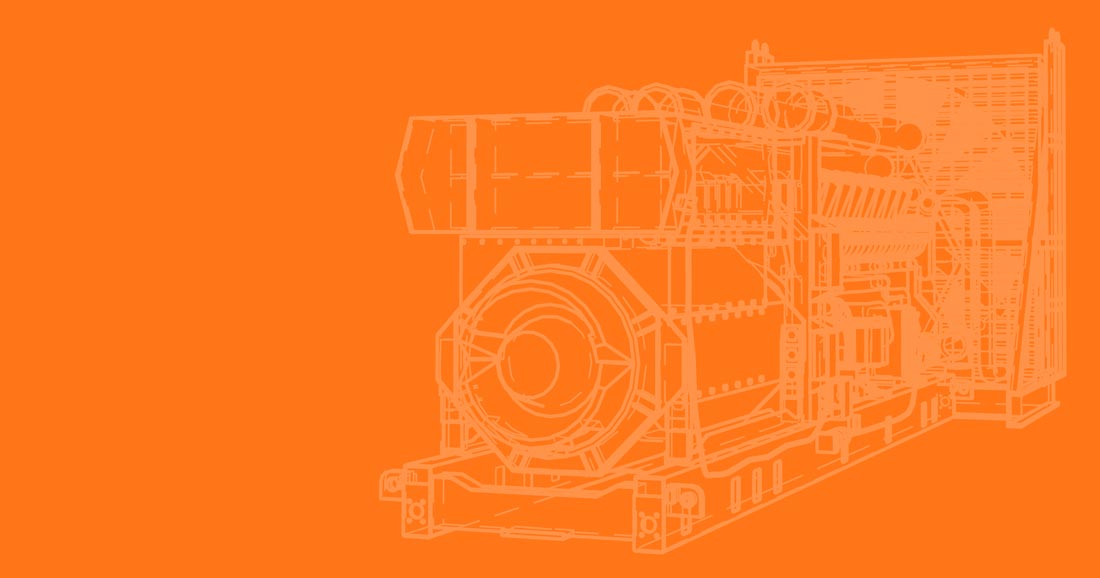
AN ADVANCED DRYING SOLUTION
Working Principle of a Tunnel Dryer
The fundamental operation of drying lanes involves systematically extracting moisture or water content from a substance. Drying lanes efficiently remove moisture from diverse materials, contributing to the preservation and processing of products. A typical drying lane designed at GEM (see the picture below), consisting of three sections: Drying Lane 1, Drying Lane 2, and Drying Lane 3.
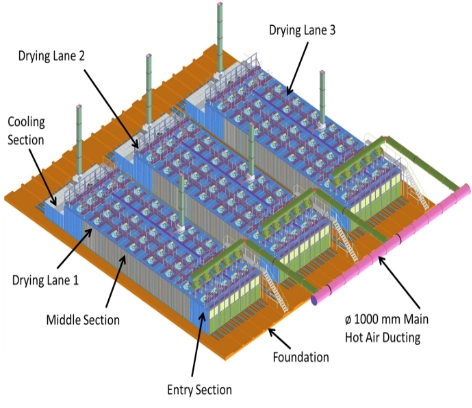
Each drying lane is segmented into three primary parts. The first, known as the entry section, is where the wet product is introduced to the drying lanes. The middle section of the drying lane, the second part, plays a critical role as the primary location for the majority of the drying process. The final section, termed the cooling section, facilitates the cooling of the dried product at a specific temperature. This involves reducing the heat, allowing the product to cool, and contributing to the preservation of its quality.
Drying lanes are precisely designed to facilitate effective air circulation around the material. This circulation is essential as it promotes evaporation by removing moisture from the material. Proper air circulation is achieved through well-designed ducting, strategically positioned dampers, recirculation and exhaust fans, creating a continuous flow of air over and around the material. As the material is exposed to controlled air circulation and temperature, moisture content within the material evaporates into the air. The moisture-laden air is then typically exhausted from the drying system.
Salient Features
- Air circulation system improve airflow and drying time
- Uniform drying of all type of materials fed as input
- Controlled material speed and residence time
- Multiple lanes possible for higher capacity
- Product moisture sensing capabilities
- Insulated construction to minimize heat loss
- Track and trolley system to move the material and perform the drying process
Advantages
- Versatality: Capable of handling a wide range of products with varying moisture content
- Space Efficiency: Compact design with drying areas up to 360m²
- Flexibility: Available in horizontal and vertical configurations to suit different spatial and processing requirements
- Scalability: Multiple configuration options including single, two, and three-stage conveyor systems
Specifications
- Drying area of a single oven upto 75-meter square with a provision of incorporating multiple ovens.
- Provision of recirculating fan for better airflow management.
- Pusher and pull mechanism for trolley movement through screw feeder.
- Maximum operating temperature upto 150 degrees Celsius.
- Sliding door movement is facilitated through hoist crane mounted at the top.
- Common exhaust header at both the feed and discharge ends.
- Shutters assembly are used to maintain airflow within the drying environment with the help of hot air ducts.
Process Flow Diagram
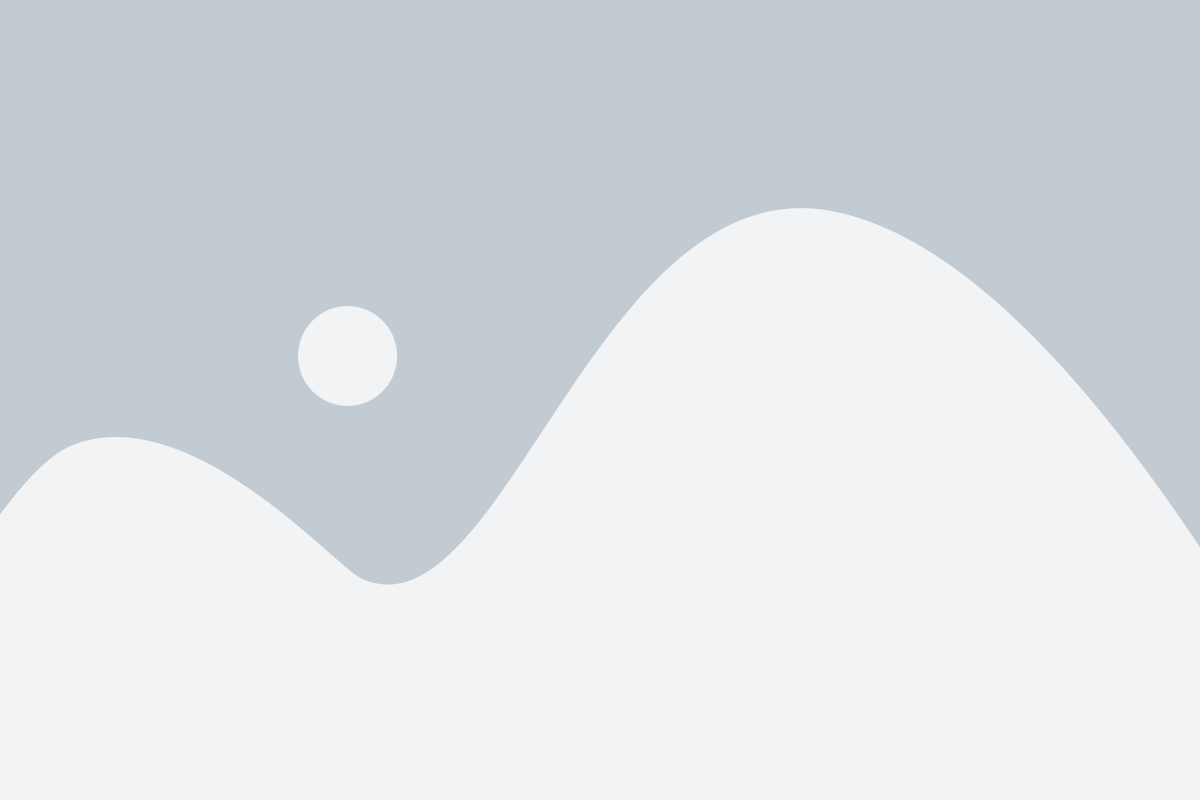
Factors Affecting Drying Rate
Application
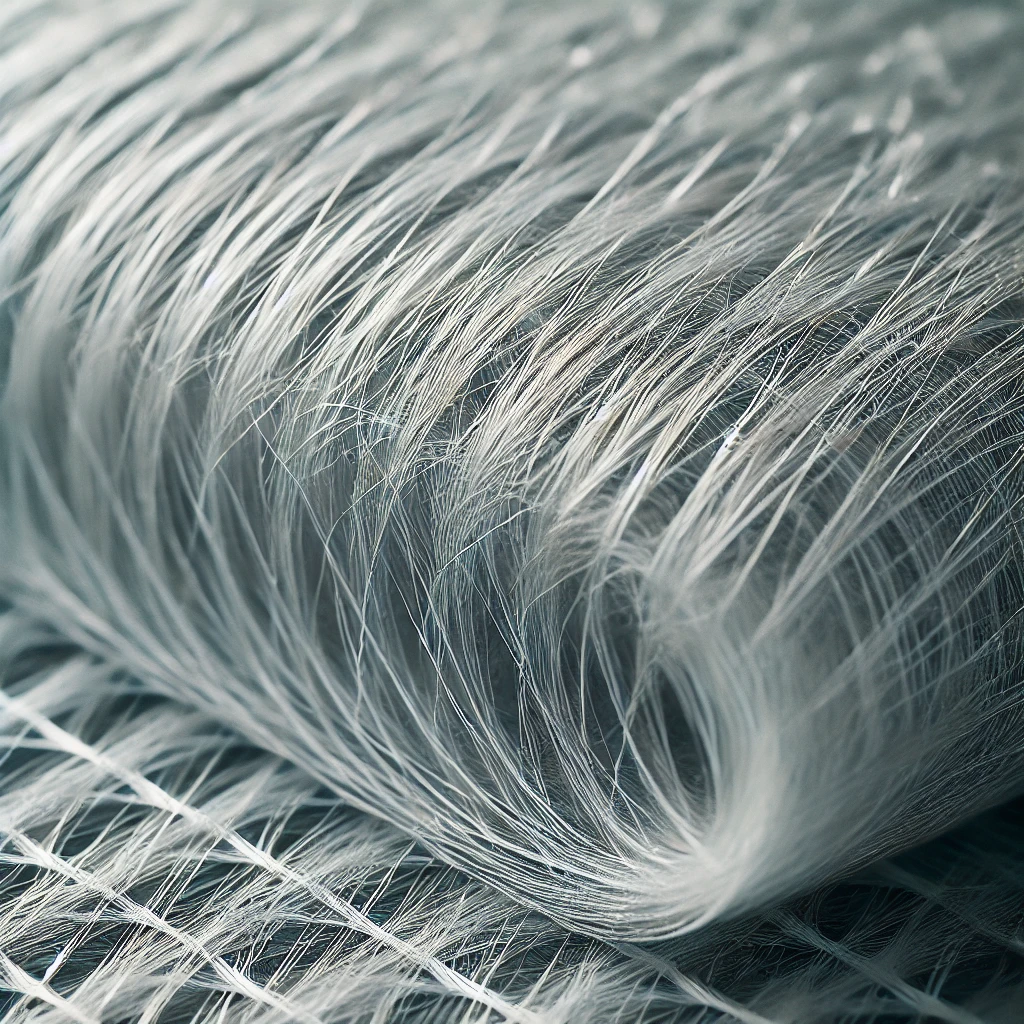
Fiberglass
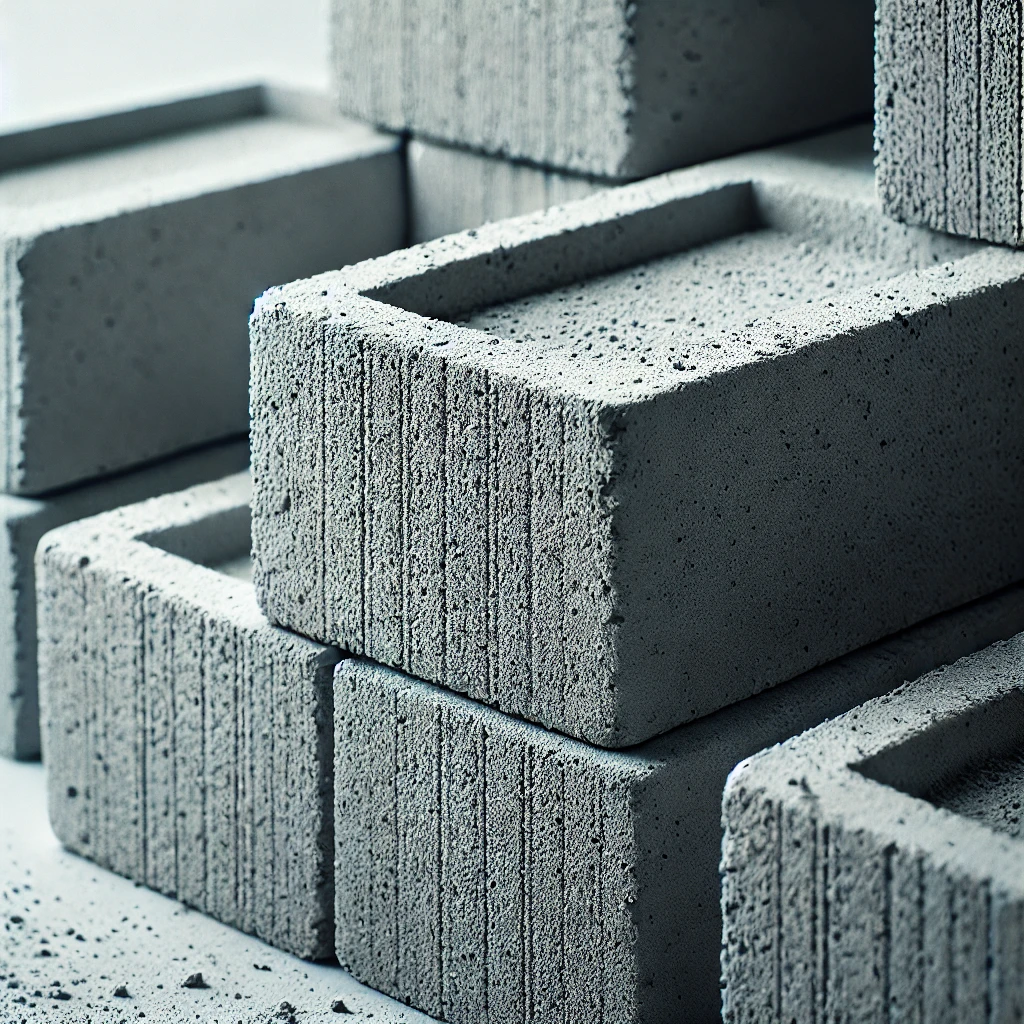
Cement Block
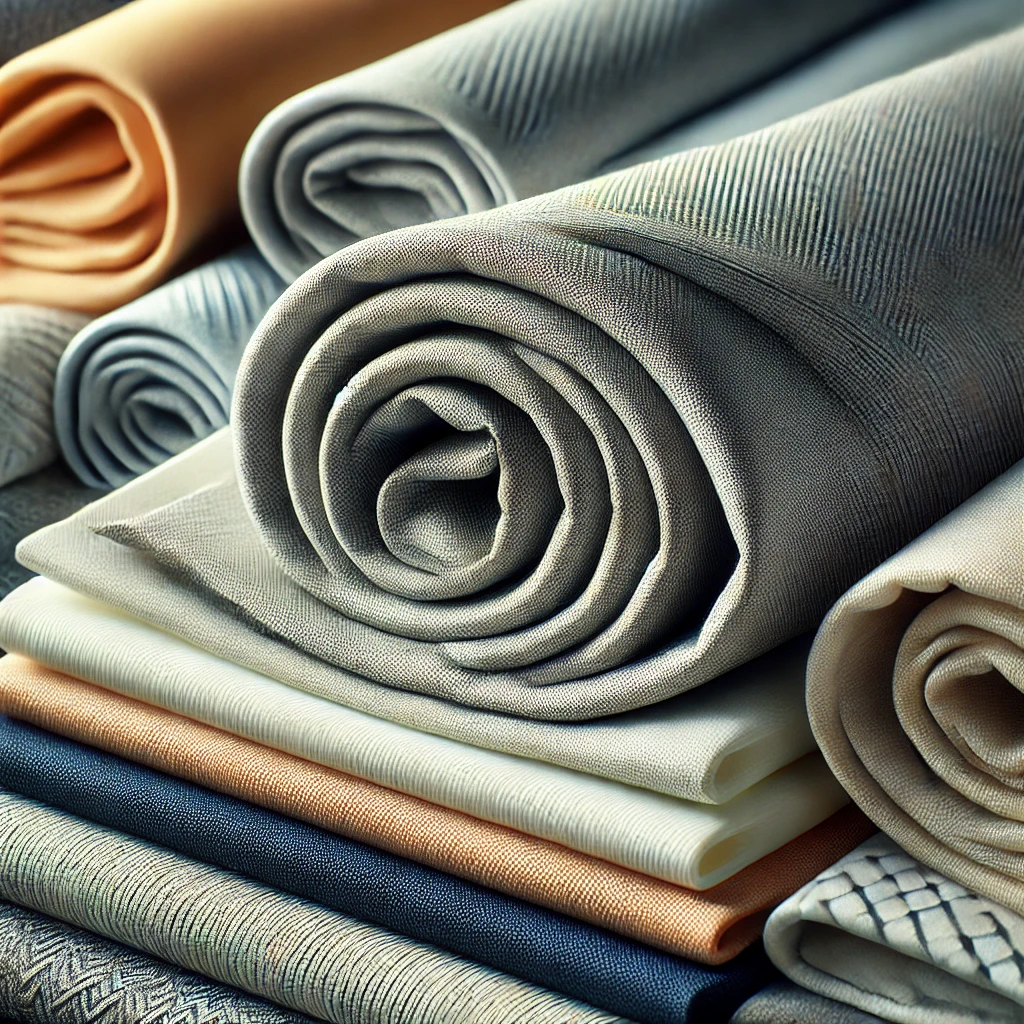
Textile Fabric
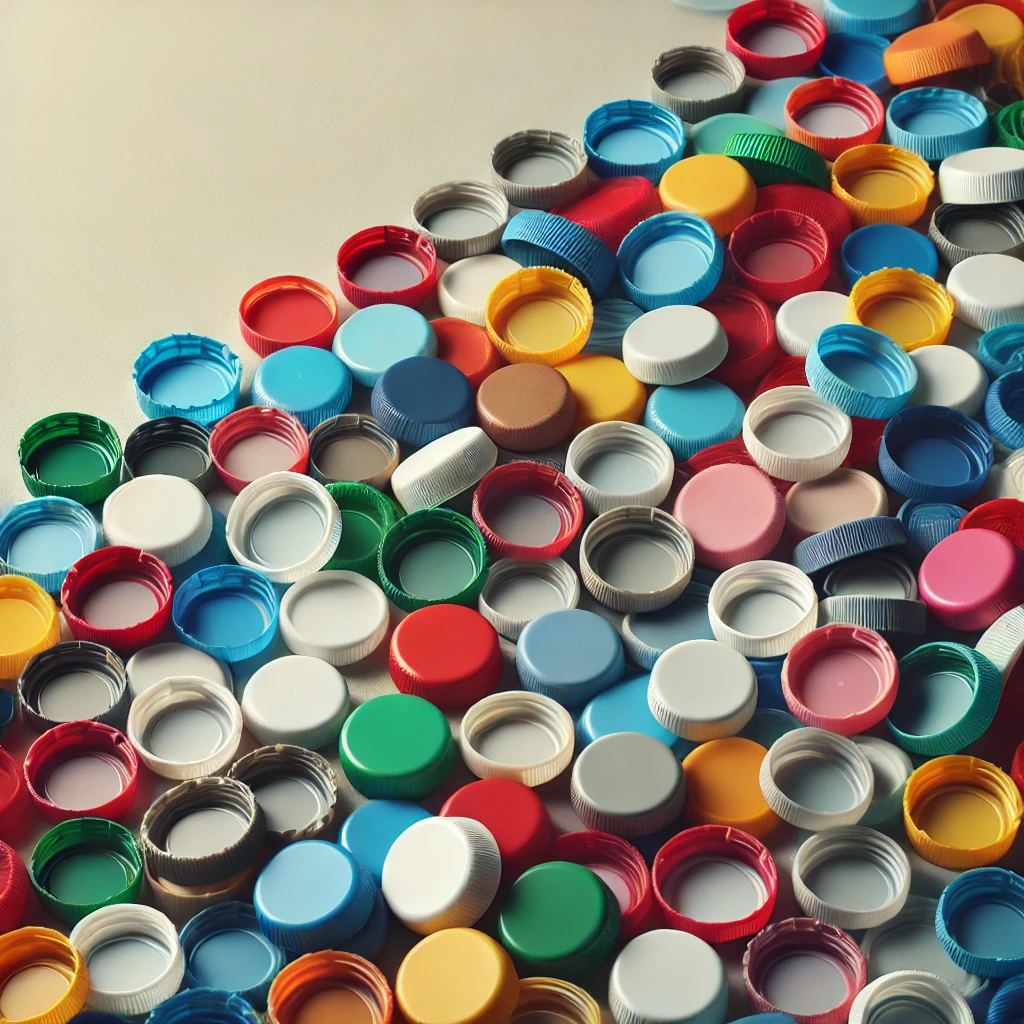
Plastic Caps

Packaging Materials
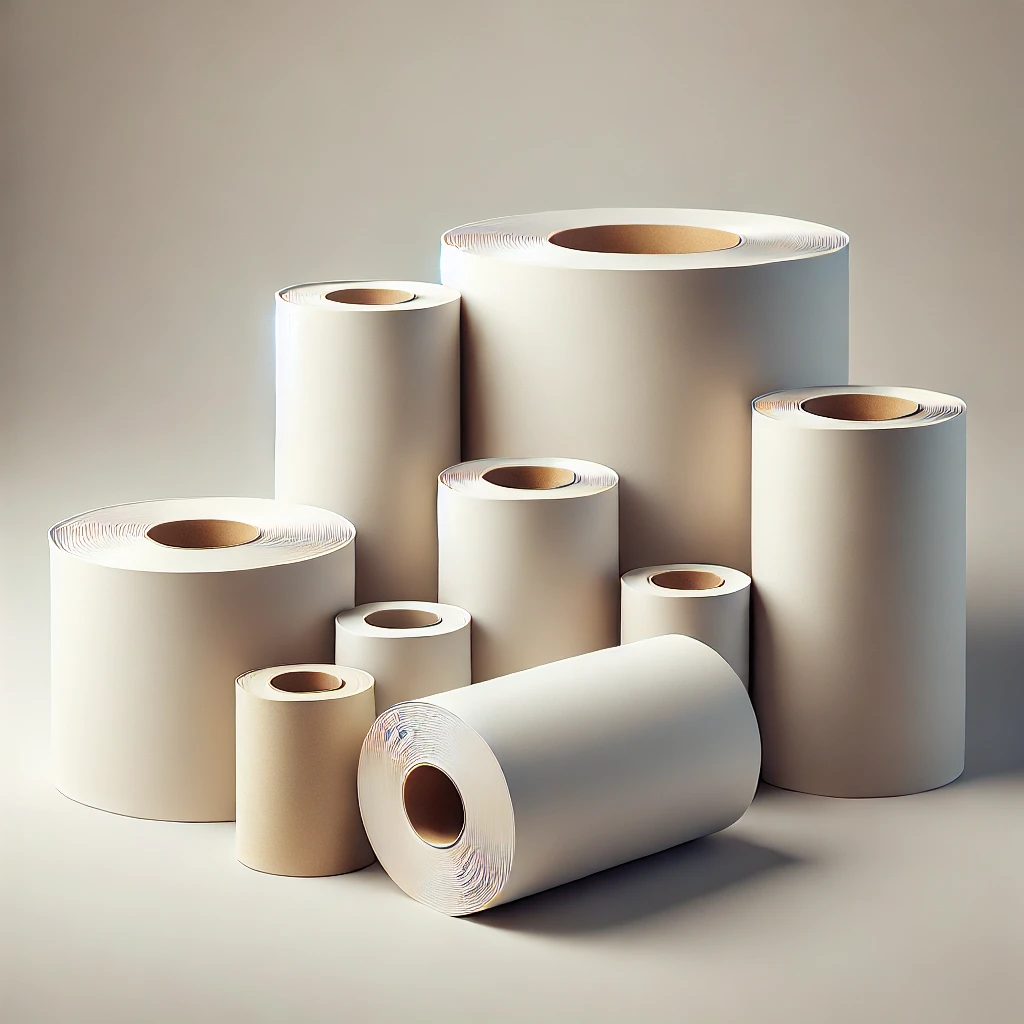
Paper
Have Questions ?